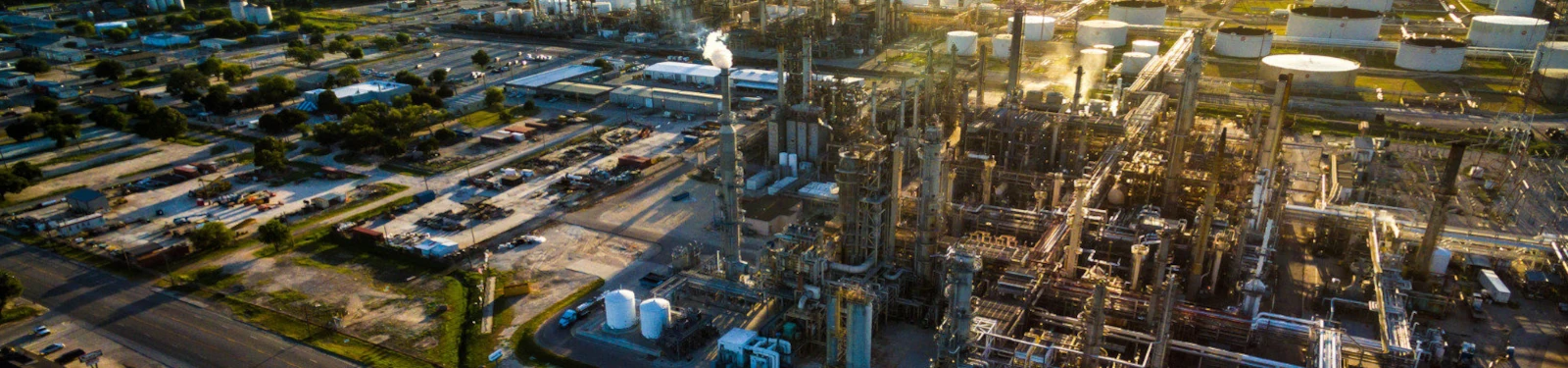

Refining
Digital transformation can safely optimize your refinery’s production and boost profitability.
Partner with PML to safely upgrade operations to meet demand while lowering operating costs, reducing unplanned shutdowns, and adapting to new regulations.
Operational flexibility is how you can enhance performance, and digital transformation is the fastest and most efficient way to achieve that goal. When you engage PML, refiners can overcome aging infrastructure, mounting maintenance costs, unplanned process shutdowns, and energy inefficiencies.
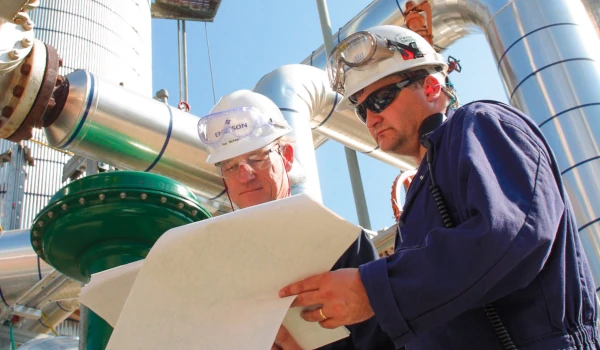
Solutions For The REfining Industry
Alkylation
CCR
Coker
Distillation & Fractionation
Fluid Catalytic Cracking
Gas Plant
Hydrogen Plant
Hydroprocessing
Sulphur Recovery
Vacuum Distillation
SAEFTY & PERFORMANCE ARE KEY
Alkylation
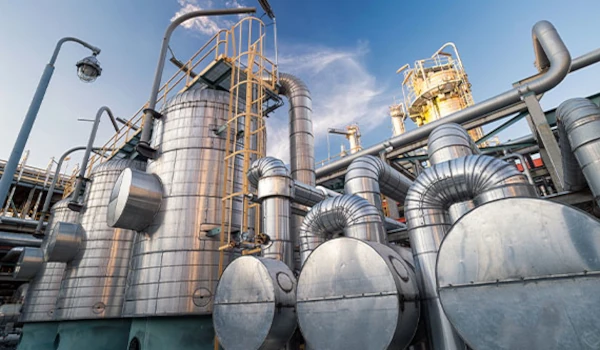
Puffer Guyana will help you detect alkylation unit problems before they escalate into safety and environmental incidents. Equipment and products durable for inhospitable and corrosive conditions are paramount to maintaining safety and environmental criteria. We offer flow and pressure control technologies that deliver the accuracy, reliability, and performance that ensures safe and optimal performance of an alkylation unit while preventing the accidental leakage of hydrofluoric acid.
RELIABLE OPERATIONS
CCR
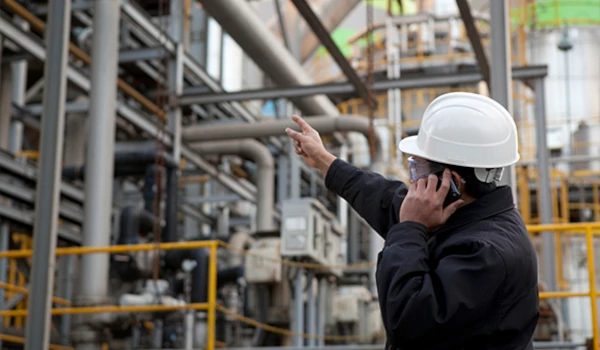
To ensure high quality products, it is important to maintain optimum performance and consistent hydrogen availability.
Catalytic reformers convert heavy naptha feedstocks from other refinery areas into the more desirable aromatic rich products for use in gasoline blending.
Solutions from Puffer Guyana allow for the reliable operation and increased availability of the catalytic reforming process.
By maintaining steady and accurate process and flow inputs, these solutions ensure that high quality catalytic reformer product is maintained.
MAXIMIZE HIGH-VALUE CUT POINTS
Coker
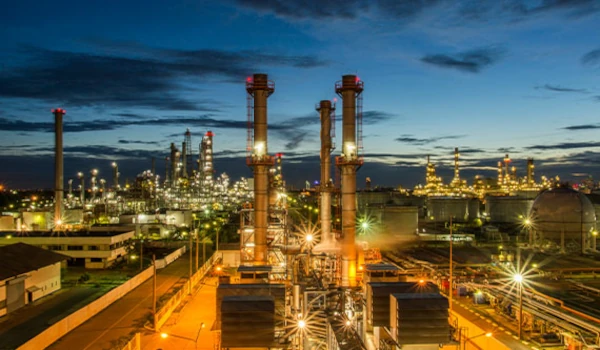
Puffer Guyana has worked with many refiners to develop solutions to some of the most difficult instrumentation and control problems in coker applications. Our team hcan help you streamline maintenance and reduce unplanned downtime caused by asset reliability issues.
The delayed coking process in a refinery is used to break down vacuum residual hydrocarbons into shorter hydrocarbon chains that can then be hydro processed into sellable products. The coker generates high temperatures and high vibration, and produces erosive petroleum coke particles that can be hard on instrumentation and erosive to piping and valves.
ACHIEVE DESIRED YIELD
Distillation and Fractionation
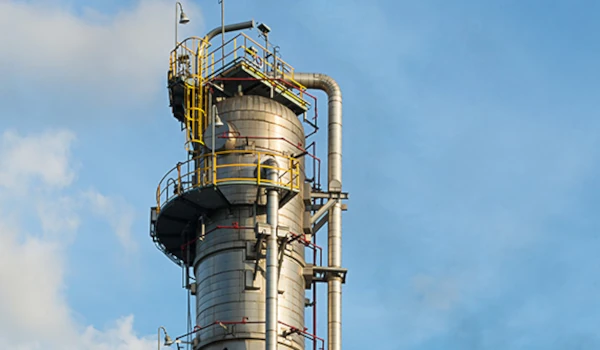
Puffer Guyana works to help you meet product specifications, minimize energy usage, and improve throughout to optimize your fractionator and distillation processes.
One of the biggest challenges of separation processing is to obtain the desired yield of sidecuts and products that meet specifications while maintaining the lowest cost and energy usage possible. Puffer Guyana team has developed control solutions for both fractionators and distillation units, ensuring the proper process control adjustment and selection of instrumentation. Let’s optimize fractionator and distillation processes to minimize disturbances, improve recovery, and increase refinery efficiency.
DISTILLATION CONTROL
Fluidized Catalytic Cracking
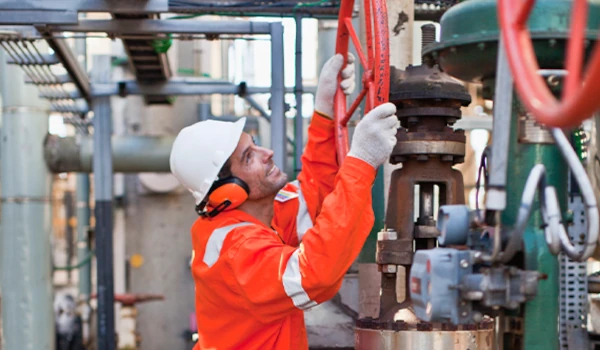
With high temperatures and severe conditions, using the proper field instrument measurements is essential to understanding how the process is performing at any given moment. Puffer Guyana’s experts have developed measurement and control solutions to ensure the unit is monitored safely, and is optimally controlled.
Fluid Catalytic Cracking (FCC) units produce refined products, such as gasoline, distillates, and olefins, through highly controlled and selective reactions in the presence of heat. The FCC unit is a critical element in the refinery and provides feedstock to several other units. It is essential that reliable, highly accurate flow and pressure control are maintained to ensure safe FCC unit operation and unscheduled shutdowns are minimized to avoid significant financial impact. Let’s reduce steam usage while maintaining quality with improved distillation control.
REACH FULL POTENTIAL
Gas Plant
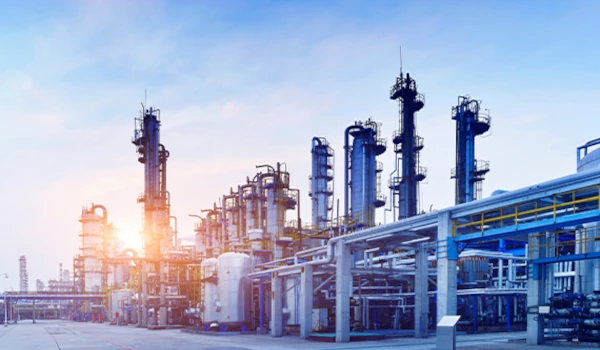
Refinery gas plants process end products into fuel gases such as hydrogen, ethane, methane, and butane. The proper selection of control components in a refinery gas plant is essential for tight containment of fugitive emissions and equipment reliability.
With proven experience in gas plant operations, our team of technical specialists assist in the proper material selection and advanced controls to optimize plants based on current market pricing.
CONSISTENT OPERATIONS
Hydrogen Plant
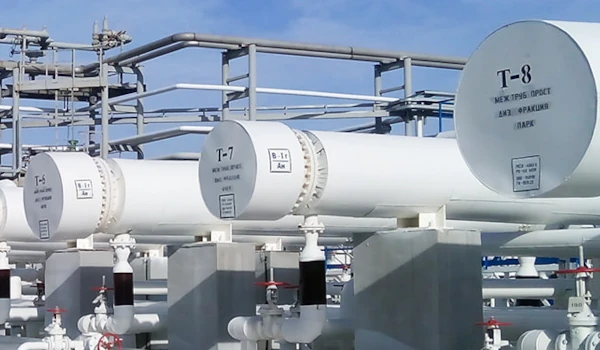
Hydrogen is essential to the hydrocracking and hydrotreatment processes used to create high value and clean products, and for the reduction in compounds that are harmful to the environment. Additionally, with the quality of crude slowly declining, the efficient use of hydrogen is essential for the profitability of the refinery.
The efficient use of hydrogen is critical in refinery operations, and you need to ensure uninterrupted and safe operation of your hydrogen supply. Puffer Guyana understands how important it is that the supply of hydrogen to the refinery is extremely reliable and safe. Our best-in-class technologies and solutions ensure that your hydrogen supply remains uninterrupted and is operated in a safe and reliable manner to reduce risk to your personnel and assets
OPTIMIZE THE PROCESS
Hydroprocessing
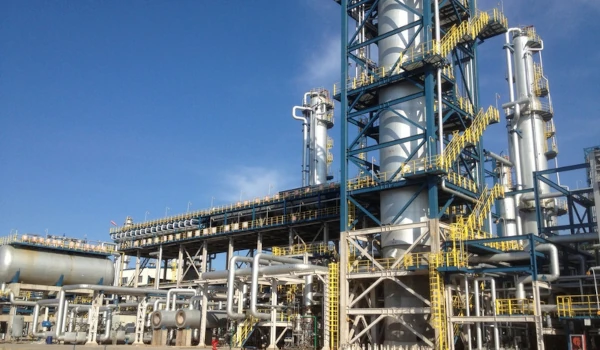
With the growing demand for clean transportation fuels, flexibility in product yields, and a shift toward low sulfur diesel, hydroprocessing has become an increasingly important refinery process. The experienced team at Puffer Guyana can recommend properly sized control valves and reliable temperature transmitters with advanced diagnostics, our experts enable enhanced insight into your processes and instrumentation.
Our top of the line technologies ensure proper control of reactor bed temperatures which lead to desired yield, increased catalyst life, and reduced temperature excursions.
MAINTAIN RELIABILITY & SAFETY
Sulphur Recovery
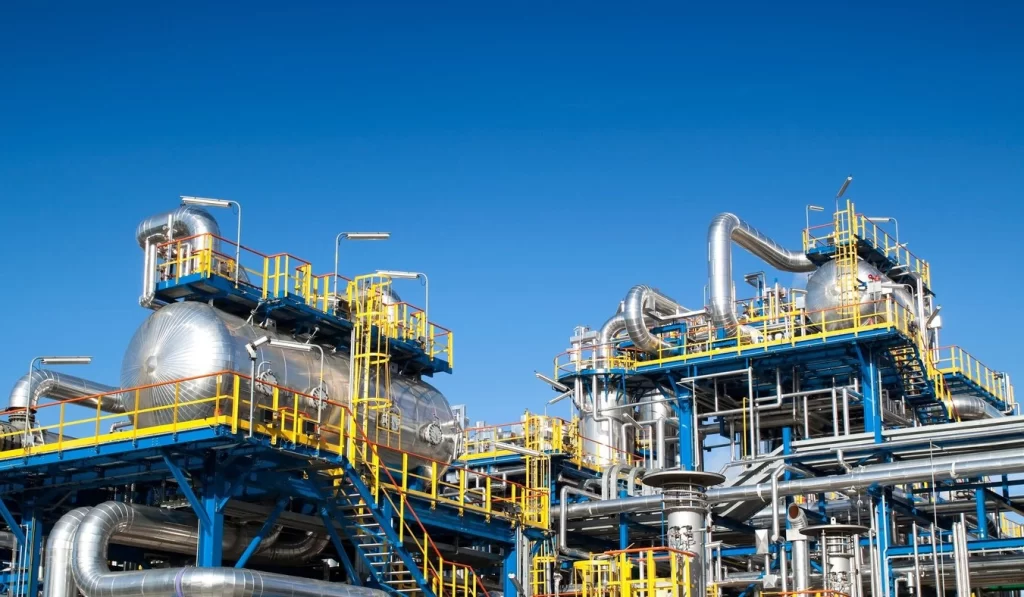
The sulfur plant is a key unit that can limit the output of the entire refinery, and up-time and safety are essential to maintain refinery throughput. The Sulfur Recovery Unit (SRU) capacity dictates what types and volumes of high sulfur feed stocks can be processed. A small gain in capacity in the SRU can yield significant profit for the refinery.
Our world-class technologies help to reduce environmental concerns by maintaining the proper ratio of H2S to combustion air to avoid the release of excessive H2S or SO2. Additionally, our experts at Puffer Guyana ensure the sulfur recovery process is executed to meet the highest reliability and safety standards.
MAXIMIZE UNIT EFFECTIVENESS
Vacuum Distillation
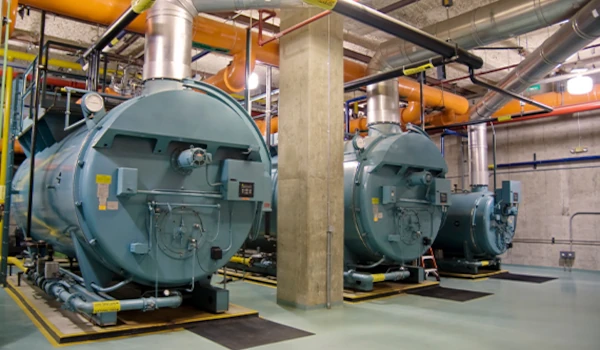
This unit is a critical element to the refinery which provides feedstock to several other units, therefore accurate and reliable flow and pressure control is essential to ensure efficient and safe operation. To improve vaporization, distillation is carried out with extremely low, near-vacuum pressures, and you can operate your distillation columns as efficiently as possible with the latest solutions from Puffer Guyana.
Our team has extensive experience with proper selection of control valves and other technologies for these applications to ensure you are able to operate your distillation columns as efficiently as possible. Additionally, our measurement and analytical technologies provide improved measurement performance and reliability.